Coalescing gas separators (or coalescing separators) are designed specifically for the removal of mist, fogs, and dust from gas streams. Standard separators cannot remove these small, minute contaminants in the gas stream because particles are usually less than 10 microns.
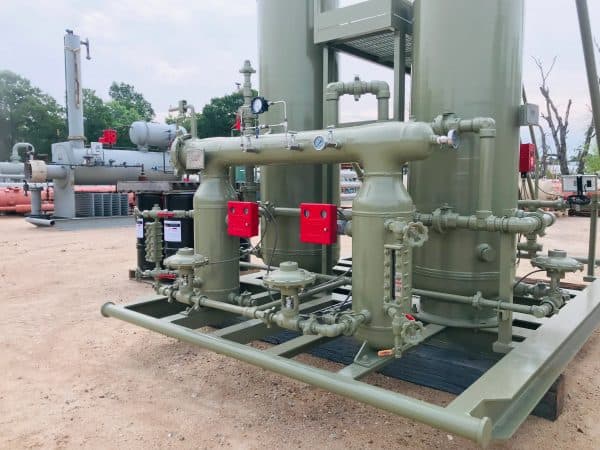
A coalescing gas separator consist of a vessel, combining specially constructed coalescing elements and a separation section with either a wire mesh or vane type mist extractor. Like a separator it also has a liquid accumulation section is provided to properly collect and discharge the liquid for further processing or disposal. Coalescing takes place as the gas passes through the filter element in the sock-type replaceable filter elements. The fiberglass forces small particles to agglomerate (coalesce) -forming larger drops or particles. The resulting larger droplets are then removed from the gas as the stream flows through the separator section. Further removal of entrained droplets is provided by the wire mesh or vanes of the mist extractor. All separated droplets are then collected in the liquid accumulation section. Any dirt, dust, rust, and scale in the gas will be removed on the outside surface of the filter elements.
Applications:
Typical application for coalescing gas separators are listed below:
- Ahead of compressors to remove dust and liquids which could cause damage to the compressor valves and cylinders.
- Ahead of dry desiccant dehydrators to prevent compressor lube, oil, fog or other liquid contaminants from entering the absorber bed and causing degradation, and excessive loss of effectiveness of the desiccant or treating media.
- Ahead of glycol dehydrators to remove compressor lube, oil, fog, saltwater, dust, rust, and scale from the gas stream and prevent contamination of the glycol solution. (Croft Production Systems considers the installation of a coalescing separator a must ahead of a glycol dehydrator when gas is to be dried following compression.
- Ahead of amine-treating units to prevent contamination of the amine solution by dust, rust, iron sulfide, scale, and liquid contaminants.
- Ahead of lean oil absorption plants to prevent contamination of the system by dust, rust, scale, and saltwater.
- Ahead of short cycle hydrocarbon recovery units to prevent “poisoning” of the desiccant.
- In the compressor fuel system to prevent plugging of the various orifices and valves.
- In refrigerant compressor discharge to recover the refrigeration compressor lube, oil, and to prevent contamination of the heat transfer surface in the process chiller or exchanger.
- Downstream of glycol absorbers or contractors to recover the entrained glycol mist carried overhead.
- Downstream of amine treating units to recover the amine solution and to prevent contamination of subsequent process equipment.
- Downstream of amine treating units to recover the amine solution and to prevent contamination of subsequent process equipment.
- Following lean oil absorbers to recover the lean oil (reducing operating costs), and to eliminate possible contamination of process equipment.
- Ahead of metering and regulating town border stations to assure long life and low maintenance of the turbine meter or standard orifice meter.
Coalescing Filter Features:
- Quick opening closure allows easy and rapid access to the filter assembly for cartridge replacement.
- All filter elements are readily accessible and can be changed quickly.
- Pressure taps are furnished to check the differential pressure drop across the coalescing elements. (Normally the pressure drop is approximately 0.5 psig with new cartridges. When the pressure drop reaches 5 to 7 psig, the cartridges should be replaced.)
- Choice of wire mesh mist extractor or vane type mist extractor.
- ASME Code construction throughout.
- Wide range of sizes and capacities are available. Large sizes, providing high capacity, are available as horizontal units only.
- High temperature filter elements are available for use with molecular sieve and short-cycle hydrocarbon recovery units.
- Models are available with a section ahead of the coalescing elements to accumulate and remove sizable quantities of free liquids.
Need to buy parts for a coalescing gas separator click here.
If you have any used coalescing gas separator for sale click here.
Need to buy used coalescing gas separator click here.
Need to buy a new manufactured coalescing gas separator click here.