Absorption vs. Adsorption
Dehydrating natural gas, or the removal of water vapor from natural gas can be done by either adsorption or absorption. Croft’s Passive Dehydration System uses adsorption, where water vapor is collected and condensed on the surface with the use of a solid desiccant. Solid desiccants have a high adsorption capacity, a low resistance to gas flow to minimize pressure drop, is both non-flammable and non-corrosive, and is inexpensive. Deliquescent salts, such as calcium, potassium and lithium chlorides, have been used by the oil and gas industries to dehydrate petroleum products for more than 70 years. These salts naturally attract and absorb moisture (hygroscopic), gradually dissolving to form a brine solution. The amount of moisture that can be removed from hydrocarbon gas depends on the type of desiccant as well as the temperature and pressure of the gas.
TEG units dehydrate by absorption, which uses liquid desiccants such as glycol, to remove the water vapor. Lean, water-free glycol is pumped to the top of an absorber where it is contacted with the wet natural gas stream. The glycol removes water from the natural gas by physical absorption and is carried out the bottom of the column. Upon exiting the absorber the glycol stream is often referred to as “rich glycol”. The dry natural gas leaves the top of the absorption column and is fed either to a pipeline system or to a gas plant.
After leaving the absorber, the rich glycol is fed to a flash vessel where hydrocarbon vapors are removed and any liquid hydrocarbons are skimmed from the glycol. This step is necessary as the absorber is typically operated at high pressure and the pressure must be reduced before the regeneration step. Due to the composition of the rich glycol, a vapor phase having a high hydrocarbon content will form when the pressure is lowered.
After leaving the flash vessel, the rich glycol is heated in a cross-exchanger and fed to the regenerator. The glycol is thermally regenerated to remove excess water and regain the high glycol purity. The hot, lean glycol is cooled by cross-exchange with rich glycol entering the stripper. It is then fed to a lean pump where its pressure is elevated to that of the glycol absorber. The lean solvent is cooled again with a trim cooler before being fed back into the absorber.
Emission Reduction in Natural Gas Dehydration
Here at Croft Production Systems, we explain the benefits of our Passive Dehydration System or PDS for companies on a daily basis. The unit is environmentally friendly. The PDS has zero toxic emissions so it requires no air permits. A company can get the units and start processing natural gas the same day if needed.
PDS units, the safe alternative to TEG units, have no moving parts or open flames, and almost no emissions. Due to the increased safety and unit’s simplicity, minimal maintenance is required for the PDS unit. Unlike the TEG units, there are no permit requirements for the PDS unit while the regulations continue to get stricter for the use of TEG units.
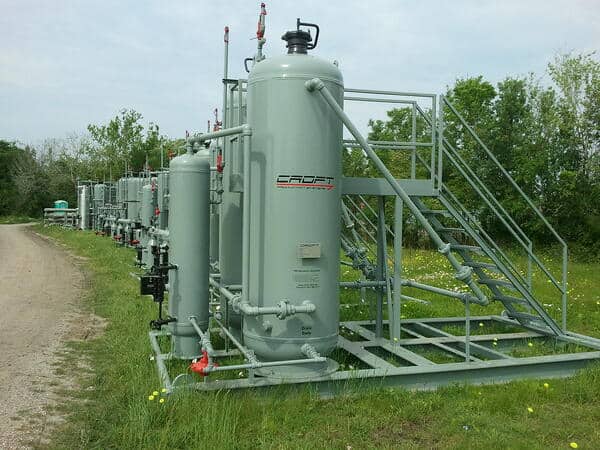
Emissions of glycol dehydration or TEG units emit both air and ground pollutants. Several known VOC’s, volatile organic compounds, such as propane, benzene, and formaldehyde occur in natural gas and are emitted from TEG units. VOC’s can cause eye, nose and throat irritation, and even damage to your liver, kidney and central nervous system [1]. Triethylene glycol, the desiccant used in TEG units, is also used in anti-freeze and brake fluid. Triethylene glycol spills kill any living organisms spilt on. TEG units also emit HAPs, hazardous air pollutants, which cause or may cause cancer and other serious health effects, including birth defects, and adverse environmental and ecological effects [2]. BTEX, or benzene, toluene, ethyl benzene and xylenes are carcinogens and are also emitted from TEG units. According to a study done by the U.S. Department of Health and Human Services, all four components of BTEX can produce neurological impairment. In addition, benzene can cause hematological effects which may lead to aplastic anemia and the development of acute myelogenous leukemia.
In addition to the HAP’s, VOC’s and BTEX emitted from TEG units, an outrageous amount of methane is also emitted. According to the EPA, methane has a 21 times greater greenhouse effect than carbon dioxide. The annual methane emissions from dehydrators alone are over 12 billion cubic feet, which is equivalent to 4.8 million tons of carbon dioxide, or 933,000 car emissions. One TEG unit emits an average of 4,562 Mcf/year of methane, being equivalent to 354 cars emissions. The EPA states a reduction in methane by 99% using a desiccant dehydrator, or PDS unit, over a glycol dehydrator. Croft’s PDS has an annual release of 23.34 Mcf/year of methane, or 0.002 cars annually. Unlike the TEG unit, all waste in a PDS unit is condensed into a non-hazardous brine solution and safely disposed of. The PDS unit allows for the conservation of natural resources, a reduction in environmental and health liabilities, eliminates permitting for air emissions, and the emissions themselves while complying with all state and federal environmental regulations.
There are several areas to upgrade or monitor on a glycol dehydrator to reduce emissions in your operations. Properly sizing the BTEX unit to capture the BTEX gases, tweaking to have a proper and consistent burn in your firetube, watching for and monitoring vented gases from improper maintenance, utilizing zero bleed controllers and instrumentation, and there is more on this topic discussed in our webinars and blogs. You can find controllers and instrumentation upgrades on our websites at www.Croftsupply.com and large equipment like BTEX units on www.Surplusenergyequipment.com.
Saving Capital in Natural Gas Dehydration
CROFT has had some potential clients asking about the cost of our PDS. Their main concern tended to be the upfront capitol in getting the unit set up, stating that it was not justified to change.
Below are 3 case studies for TEG’s that have been replaced with a CROFT Passive Dehydration System. The cost numbers that are with them only included money gained from a reduction in gas losses. These clients saw even greater savings from not having to buy replacement parts or pay for repairs on the TEG’s. Also with CROFT’s service team handling maintenance, these clients spend much less time in the field dealing with the ongoing issues TEG’s have.
PDS Case Study #1
The first site is located south of Victoria Texas. The well parameters are an average of 125 MCFD, 600 PSI, 100*F. CROFT replaced an old oversize TEG with a single Model 20″ PDS. The unit rental fee and monthly enviroDRI cost equaled $750-$800 per month. The client saw an average increase of 25 MCFD after our unit was brought online to an average of 150 MCFD. That 25 MCFD increase at $3.00 per MCF creates a gross revenue increase of $2,280 more per month and subtracting our monthly cost at $800 it is a $1,480 increase.
PDS Case STUDY #2
The second is a sales point located south of Miranda City, Texas. Well site parameters are an average of 500 MCFD, 1050 PSI, 100*F. CROFT replaced an old TEG with a dual vessel PDS skid. Rent and monthly enviroDRI cost equaled $1,400-$1,500 per month. The client saw an increase of 30-40 MCFD after our PDS was brought online. At 30 MCFD increase at $3.00 per MCF a gross revenue increase of $2,736 more per month and subtracting our monthly cost of $1,500, it is a $1,236 increase.
PDS CASE STUDY #3
The third well site is located in south Texas. This Unit had a glycol dehydrator and after the first five months of production, the volume had declined to about 10-15 MCFD. The wellhead pressure would decline below the acceptable minimum and the well would be shut in for a few days and then brought on for a few days. It was determined that the glycol unit was consuming a large amount of gas and the decision was made to swap the unit for a Croft PDS. The PDS was brought online in January and stabilized production at a consistent 10-15 MCFD higher average. In the chart below you can see that production was flat and the well no longer needed to be shut-in to build pressure. Our Croft PDS unit greatly reduced the amount of client time on location and at a 10 MCFD increase and $3.00 per MCF our client saw a gross revenue increase of over $900 and subtracting our monthly cost at around $500 it is a $400 increase.
Learn more about Croft Production Systems Passive Dehydration Systems or check our information video below for a better understanding of PDS operations.
*Updated May 2020 by CROFT Representative
- 2012, “An Introduction to Indoor Air Quality (IAQ),” Environmental Protection Agency. http://www.epa.gov/iaq/voc.html#Health_Effects
- 2012, “Pollutants and Sources,” Environmental Protection Agency.http://www.epa.gov/ttn/atw/pollsour.html
- S. Bosch, S. Wilbur, 2004, “Interaction Profile For: Benzene, Toluene, Ethylbenzene, and Xylenes (BTEX),” U.S. Department of Health and Human Services. http://www.atsdr.cdc.gov/interactionprofiles/IP-btex/ip05.pdf