Picture this…
You are asked to come out to a well site and check out some of the equipment. Once you get there, you look left, you look right and you see nothing. There is absolutely nothing around and the only “address” to the well site are GPS coordinates. Yet, all of the equipment to drill and process are still properly operating. Where is all of this equipment getting power to operate? Is there even any power our here? Great question!
What are Natural Gas Generators?
Ladies and gentleman, I would like to introduce you the generator. Generators are the solution for the oil and gas industry because they allow well sites to continue drilling and production where electricity is not available or present. Whether it is a generator that helps power frac equipment or a light tower generator that is providing lighting for the well sites, generators are an instrumental piece of equipment for the proper (everyday) function for a well site in oil and gas industry.
Many generator companies are gearing towards the use of natural gas generators. This way, the generators are able to utilize the natural gas straight from the wellhead as instrumentation gas; making it a more convenient, efficient and unlimited clean-burning fuel source.
Fueling Natural Gas Generators
Natural gas generators cannot always be hooked up and ran straight from the wellhead. Running generators on raw or unprocessed gas can be detrimental and cause permanent damage to the engines. For example, well gas may contain a gas composition that is too sour, wet, or rich for the generator engines. Generators need treated gas in order to fuel the engines properly.
See, raw gas straight from the wellhead can contain different compositions. If you were to plug the generators straight from the wellhead and begin running with raw gas, it can seriously damage the generators. What could possibly be in this gas that is so bad? I am glad you asked!
H2S, water, particulates, oh my!
Sour gas is when natural gas contains H2S in the gas stream. H2S is detrimental to equipment and causes corrosion so removal of H2S for natural gas generators is extremely important. Not only is H2S horrible for equipment, it is also deadly and dangerous to humans. Without a doubt, H2S is an important element that needs to be treated for.
Water in the gas stream can cause freeze-ups and corrosion of equipment. Along with water, rich gas and high BTUs of the gas stream can also damage generator engines. These generators to need run off the gas that has been treated of particulates, free liquids, water, H2S, and heavy hydrocarbons to provide a safe and stable fuel for the natural gas generators. CROFT’s FCS-100, PG-100, PG Low pressure, and CIS-100 are all tailored for fuel gas as they process raw natural gas providing safe gas that has been treated for the generators. Check out our product line and contact us to learn more about how CROFT’s units assist with natural gas generators!
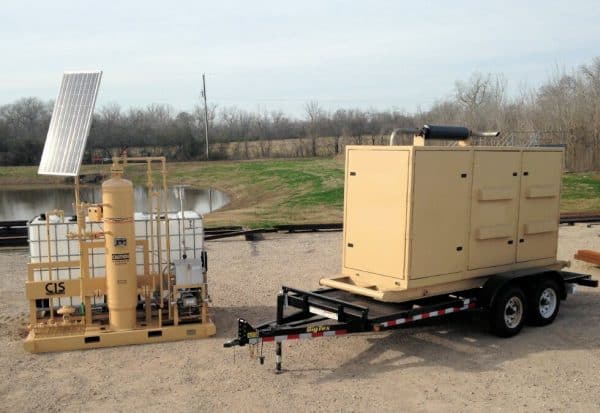