The US shale sector has been driven by the pressure pumping units that take the theory of hydraulic fracturing and put it into practice. Revolutionary at the time but in the past 2 decades, these high-horsepower machines have seen relatively scant technological advancement.
Advancement usually happens in times of scarcity and that is what is happening. With the industry downturn, profit margins are tighter and the need for longevity is required for ROI. These downturns have propelled subject matter experts in the industry to go back to the drawing board focusing on pressure pumping technology.
Companies have innovated in converting their fleets to partial or fully natural gas powered frac fleets or electric fleets. These natural gas-powered fleets p The Ideal eFrac fleet provides an environmentally and socially responsible fracturing option that minimizes sound and carbon emissions, offers a clean and simple rig up, and significantly increases power density while maintaining the redundancy that efficient frac operations require. This solution seems to be the logical next step for the future to be cost-effective and environmentally more responsible.
The Challenge of Using Field Gas:
Past Challenge: Stimulating an unconventional reservoir requires a lot of horsepower, which means burning a lot of diesel fuel in a conventional frac fleet. Even a small spread consumes around 9,500 gallons of diesel each day, costing near $30,000. Additionally, diesel-powered pumps dictate the construction of large and expensive well pads. As a rule, a single fleet needs up to three times the area of a drilling rig. But in converting to an e-fleet the challenge of the diesel supply chain is reduced or goes away.
Description | Inlet Parameters | Outlet Parameters |
Gas Volume | 400,000 cf/h | Same |
Gas Temperature | 105 | >70*F |
Gas Pressure | 1000 PSI | 250 PSI |
H2O (Lbs/MMcfd) | Fully Saturated | <4 LBs |
Heavier Hydrocarbons | Proprietary | Proprietary to Vendor |
Current Challenge: When converting to 100% natural gas-burning turbines to feed the hydraulic fracturing pumps that natural gas needs to be processed properly or the whole operation fails. Finding a source of natural gas clean enough to go directly into an engine can be difficult and even the cleanest natural gas out of a well will still require some cleanup before it enters the engine. So to remove this restriction of only processed gas the system must be designed to deliver the best economics by using unprocessed or lightly processed field gas that can be piped directly to the pad from producing wells or associated gas systems, which could help operators dial back flaring.
The focus of this case study is CROFT’s Fuel Gas Conditioning System with a Natural Gas Powered Frac Fleet client to assist in conditioning the unprocessed fuel gas from the field allowing for a substantial reduction in Diesel cost.
Below are the parameters of this large natural gas powered frac fleet.
The Solution for Natural Gas Driven Frac Fleets
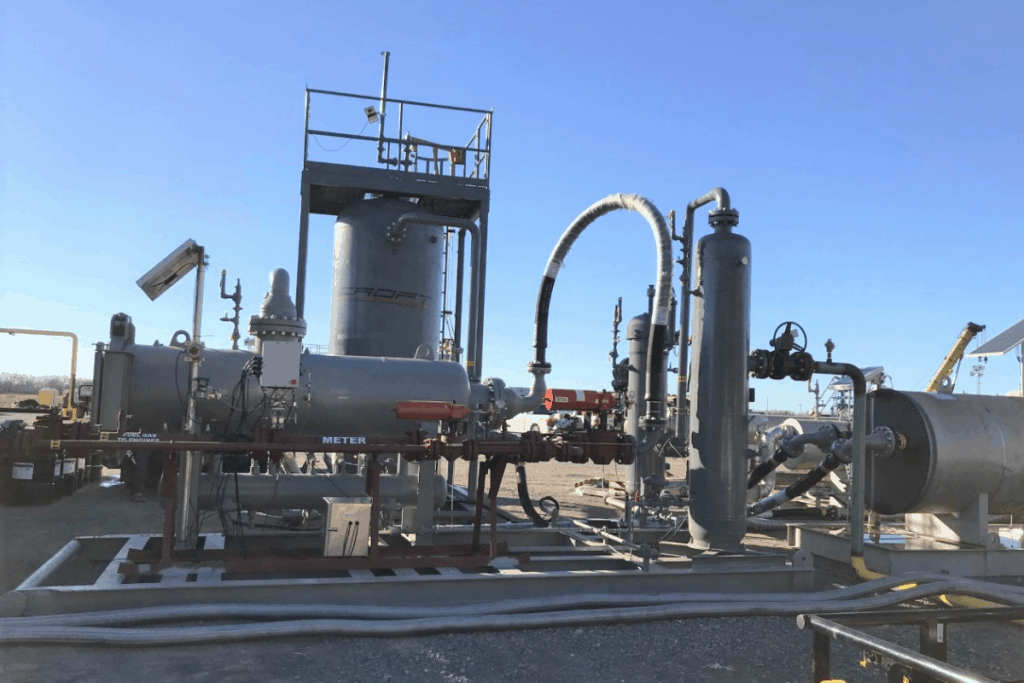
CROFT worked with e-fleet client and turbine generator engineers to determine the unprocessed gas coming into the fleet and what is required on the outlet of our equipment before entering the frac fleet. Once we had preliminary design work of the equipment required to get the job accomplished CROFT then has to work the designs with manufacturing groups and the service personnel that will work on the fleet. Then there were some extreme time constraints of 6 weeks to get all equipment ready.
CROFT engineers put together a solution that will work in processing the gas with operational safety factors of unknown future variables, meeting service operation efficiency, and time constraints to meet the frac fleet schedule.
Required equipment below:
Passive Dehydration System: CROFT has the PDS as a solid desiccant dehydrator that is safe, easy, and effective in dehydrating the gas stream utilizing the adsorption process. Working with the client’s parameters, we properly sized the system required to meet outlet specs. CROFT engineers sized the system to handle the 3-4 weeks of timing without service and to distribute flow in order to decrease the probability of any pressure differential across the system.
JT plant: The Joule Thomson Systems, also known as a JT skid or a JT plant, simultaneously reduces the water dew point of gas, recovers valuable hydrocarbon liquids, and lowers the BTU of the gas stream to sales contract specifications or levels suited for high-speed engines.
Coalescing Filters: Coalescing gas separators are designed specifically for the removal of mist, fogs, and dust from gas streams. These contaminants usually exist with the bulk of the particles having diameters considerably less than 10 microns; therefore, standard separators or scrubbers are not capable of effectively removing these minute/small particles. These filters are consumables and do need to regularly be changed out, especially if a pressure differential occurs, so buy replacement filters.
Line Heater: Indirect Line Heaters are used with high-pressure natural gas streams to counteract the Joule-Thomson (JT) effect where a reduction in temperature occurs at the choke when the well stream pressure is rapidly reduced to sales line pressure or in this case production equipment pressure. Upgraded to utilize a burner management system to reduce downtime.
Separators: Separators are mechanical devices for removing and collecting liquids from natural gas. Most common separators are cylindrical vessels that separate oil, gas, and/or water from a well. CROFT manufactures separators in either horizontal or vertical separators and in two-phase or three-phase. It is important to have proper separation in order to protect slugging and particulates from entering and fouling downstream processing equipment.
Meter: Meter Run for field metering and skid package integration. This was a high-end custom package with all the bells and whistles we can offer to integrate all systems and utilize an ESD switch. These skids are built with high-quality components assembled to exacting tolerances meeting or exceeding API, ASME, and AGA requirements.
Benefit:
The package system has limited burners, and vents a minimal amount of emissions and CROFT was able to deliver equipment within 6 weeks of the signing of leasing contracts. CROFT personnel were able to provide startup assistance and get the system going within 24 hours of delivery. The system was modular designed, along with high-pressure flex hoses so drawings were sent to the client’s 3rd party crew to start the piping immediately when delivered. The system’s desiccant is only utilized when flowing so when the full flown was switched over the outlet dewpoint decreased from full saturation lbs/MMcf to <2lbs/MMcf.
Result:
Without interruption, this system is handling the volume swings, saturation swings from pressure and temperatures, and maintaining an outlet dewpoint and hydrocarbon dewpoint. Once proven that the equipment works for the entirety of the 12-month project, the clients plan to purchase custom trailers from CROFT to stay with their frac fleet.
Learn more about our Fuel Gas Conditioning System.