What is a Separator?
An oil and gas separator is used for removing and collecting liquids from natural gas. A properly designed separator will also provide the release of entrained gases from the accumulated hydrocarbon liquids. To learn more, check out our blog, “What is a separator? “.
The Separation Process
All separators have at least three, and usually four sections comprising the separation process. The primary separation section is the portion of the vessel around the inlet where the energy of the gas entering the well stream is dissipated. The area of the separator immediately beyond the inlet deflector, between the liquid accumulation section and the mist extractor is called the secondary separation section. In this section, the velocity of the gas and liquid is reduced because of the increased cross-sectional area. All separators must provide an area where the collected liquid from the primary separation section, the secondary separation section, and the mist extractor can be held for a short period of time and then dumped into storage. The three types of mist extractors most commonly used in oil and gas separators are knitted wire mesh, vane, and centrifugal. Mist extractors cause small minute particles to form into larger droplets. As the gas stream passes through the mist extractor, the surfaces of the mist extractor itself are wetted with the entrained liquid particles. To learn more, check out our blog “How Does a Separator Work?“
When do you utilize a Horizontal Separator?
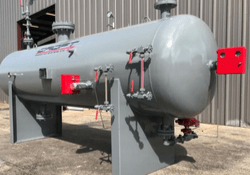
- Areas where there are vertical height limitations
- Foamy production where the larger liquid surface area available will allow greater gas break-out and foam breakdown
- Three-phase separation applications for efficient liquid-liquid separation
- Upstream of process equipment which will not tolerate entrained liquid droplets in the gas
- Downstream of equipment causing the liquid formation
- Well streams having a high gas to oil ratio and constant flow with little or no liquid surges
When do you utilize a Vertical Separator?
- Well streams having large liquid to gas ratios
- Well streams having sizable quantities of sand, mud, or other related substances
- Areas having horizontal space limitations, but little or no vertical height limitations
- Well streams or process flow streams which are characterized by large instantaneous volumes of liquid
- Upstream of other process equipment tolerating essentially no entrained liquid droplets in the gas
- Downstream of equipment causing liquid formation
What is a Free Water Knockout?
Freewater Knockouts are bulk liquid knockouts and generally do not have mist extractors. Typically the gas phase is recombined with the oil phase and the water phase is dumped elsewhere. If the oil phase is not recombined with the gas and is discharged separately the vessel is not a free water knockout but a three-phase separator.
What is Stage Separation?
The purpose of Stage (Not Phase) separation is to reduce the pressure on the separated liquids a little at a time, in steps, or stages, so that it will result in a more stable liquid that doesn’t give off gas.
Petroleum liquids at high pressures usually contain large quantities of liquefied propanes, butanes and pentanes, which will vaporize or flash as pressure is reduced.
Can a Separator Have Carry Over?
A phenomenon in which free liquid leaves with the gas phase at the top of a separator. Carryover can indicate high liquid level, damage of the separator or plugged liquid valves at the bottom of the separator.
What is a Liquid Slug?
A liquid slug is a type of flow in which surface equipment may be damaged by the sudden impact of a liquid slug in a phenomenon called water hammer.
Learn more about CROFT Separators or Request a Quote.